Development of a Marmoset Apparatus for Automated Pulling to study cooperative behaviors
Figures
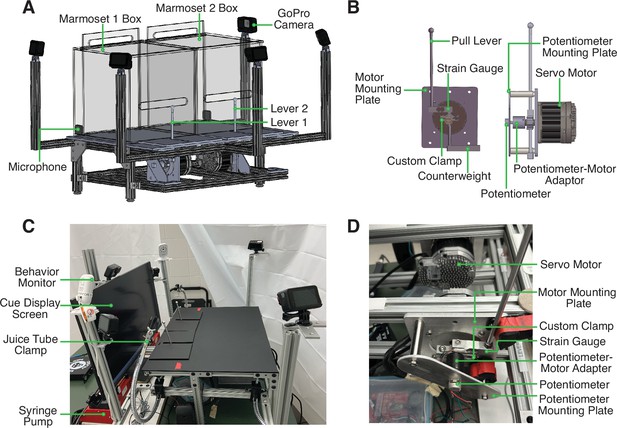
Design and Structure of Marmoset Apparatus for Automated Pulling (MarmoAAP).
(A) CAD model of apparatus highlighting general apparatus layout, transparent testing boxes, frame structure, video cameras, and microphones. (B) CAD model of lever-motor assembly. Left: Side view of lever-motor assembly. Potentiometer-motor adaptor has been omitted in this view due to its obstruction of view of other components. Right: Front view of lever-motor assembly. (C) Photo of actual apparatus. (D) Photo of lever-motor assembly.
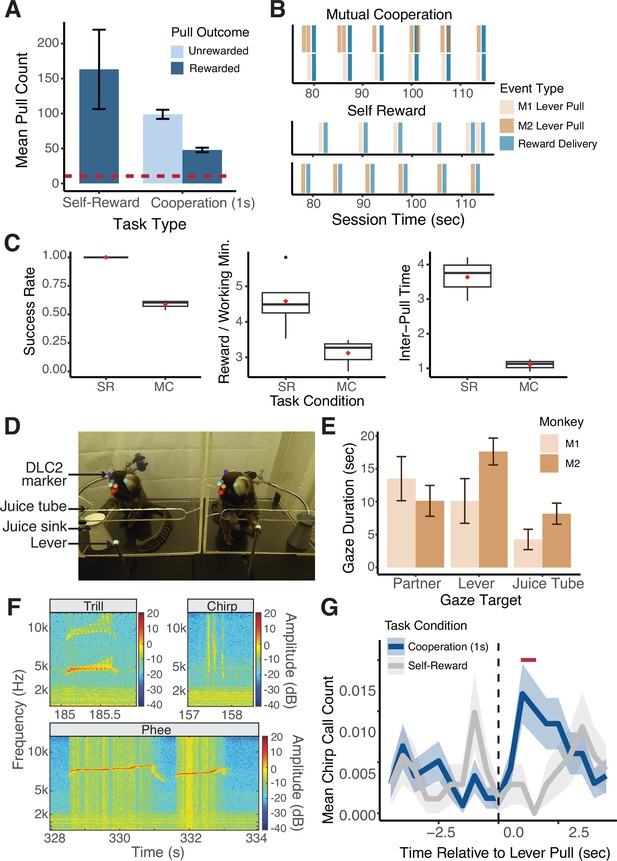
Quantitative behavioral measurements with Marmoset Apparatus for Automated Pulling (MarmoAAP).
(A) Quantification of average number of lever pulls performed per animal in Self-Reward and 1 s Mutual Cooperation sessions (mean ± s.e.m.; n = 10 Self-Reward sessions, 67 Cooperation sessions). Red dashed line indicates the average number of trials collected per session from a sample of non-automated cooperative pulling paradigm experiments (Cronin et al., 2005; Martin et al., 2021; Mendres, 2000; Plotnik et al., 2011; Range et al., 2019; Drea and Carter, 2009; Seed et al., 2008). (B) Event time series example from a Mutual Cooperation and Self-Reward session. Each bar represents a task-related event (tan: monkey 1 lever pull, brown: monkey 2 lever pull, blue: reward delivery). (C) Metrics quantifying performance on MarmoAAP from six example sessions (three Self-Reward, three Mutual Cooperation). Red diamond indicates the mean. Left: Success rate calculated as number of successful lever pulls divided by number of total lever pulls in a session. Middle: Rewards earned per working minute calculated as the average number of rewards earned in 60 s for cumulative time in a session in which a monkey had pulled a lever within 30 s of that time. Right: Inter-pull time calculated as the average amount of time between M1 and M2 lever pulls in a session. (D) Example of DLC2 labeled video frame as marmosets perform cooperative pulling task. (E) Quantification of gaze targets averaged across three example cooperation sessions (mean ± s.e.m., n = 2 marmosets with 4 sessions each). (F) Example vocalizations captured during behavioral sessions. (G) Peristimulus time histogram (mean ± s.e.m.; n = 1103 Cooperation lever pulls, 566 Self-Reward lever pulls) of chirp vocalizations from one marmoset across Self-Reward (gray) and Mutual Cooperation (blue) sessions. Red bar indicate time bins with significantly different call counts for Cooperation compared to Self-Reward task conditions (Wilcoxon rank sum test, p < 0.05).
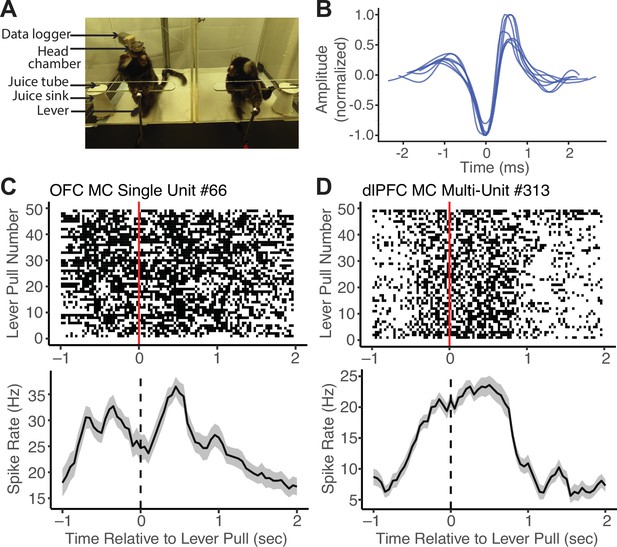
Wireless neural data recordings with Marmoset Apparatus for Automated Pulling (MarmoAAP).
(A) Photo of marmosets performing Mutual Cooperation task with one marmoset performing the task with a head-mounted wireless recording system. (B) Example single-unit waveforms from one recording session of the orbitofrontal cortex (OFC). (C) Top: Peristimulus time histogram of an example single OFC neuron averaged across all self lever pulls in one session aligned to the time of lever pull registration (dashed line) (n = 49 lever pulls, bin size = 150 ms with 50 ms sliding window). Bottom: Raster plot of the same example OFC neuron relative to all self lever pulls (red line = lever pull registration) in one example session. (D) Top: Peristimulus time histogram of an example dorsolateral prefrontal cortex (dlPFC) multi-unit averaged across all self lever pulls in one session aligned to the time of lever pull registration (dashed line) (n = 49 lever pulls, bin size = 150 ms with 50 ms sliding window). Bottom: Raster plot of example dlPFC multi-unit relative to all self lever pulls (red line = lever pull registration) in one example session.
Tables
Apparatus parts and information.
Apparatus item | Part | Manufacturer/part number | Function |
---|---|---|---|
Pull Lever Head | Ball Head | Custom | Lever grip suitable for marmosets |
Pull Lever Shaft | 6-inch rod | ThorLabs / ER6-P4 | Holds lever head at appropriate height |
Lever Bumpers | Load-Rated Threaded Bumper | McMaster-Carr/93115K121 | Bumper for lever to rest on when in starting position |
Lever Assembly Motor | Servo Motor | ClearPath Integrated Servo System by Teknic/CPM-MCVC-3411S-RLN | Exerts rotational force on the lever |
Motor Mounting Plate | Custom-designed aluminum mounting plate | Custom designed. Aluminum cut by water jet | Holds servo motor to base frame |
Potentiometer | Rotary Potentiometer—10k Ohm, Linear | SparkFun Electronics/COM-09939 | Delivers real-time positional output of pull lever |
Strain Gauge | Load cell | SparkFun Electronics/SEN-14729 | Delivers real-time force reading of pull lever |
Potentiometer-Motor Adaptor | Custom designed | Custom designed. Aluminum cut by water jet | Yokes potentiometer shaft and motor shaft |
Potentiometer Mounting Plate | Custom-designed aluminum mounting plate | Custom designed. Aluminum cut by water jet | Holds the potentiometer in position adjacent to the servo motor |
Potentiometer Plate Crossbars | Ø1/2" Optical Post, SS, 8–32 Setscrew, 1/4"-20 Tap, L=2" | ThorLabs / TR2 | Fixes potentiometer mounting plate to motor mounting plate |
Counterweight | Custom-designed aluminum bar | Custom-designed aluminum bar cut by water jet | Offsets pull lever weight to balance system |
Control board | Teensy 3.2 USB Development Board | SparkFun Electronics/DEV-13736 | Microcontroller used to integrate motors, potentiometer, and strain gauge |
Breadboard | Solder-able Breadboard | SparkFun Electronics/PRT-12070 | Connects Teensy microcontroller to sensors, facilitating control and computer integration |
Syringe Pump | Syringe Pump | New Era/DUAL-NE-1000X | Syringe pump controlled by task code to deliver juice reward |
Frame | T-slotted rails | McMaster-Carr/47065T553 | Provide a scaffolding to support lever-motor assembly |
Cameras | Go-Pro Cameras | Go-Pro/HERO10 | Record videos of marmosets performing the task |
Audio Recorder | Voice Recorder, 16 GB | QZTELECTRONIC (via Amazon) | Record vocalizations from marmosets performing the task |