Researchers have successfully bulk-produced fat tissue in the lab that has a similar texture and make-up to naturally occurring fats from animals.
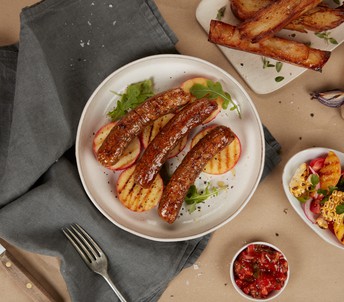
Researchers have successfully created fat tissue in the lab that may help give lab-grown meat, like these sausages, a more realistic texture and flavour. Image credit: Public domain
The results, described in a study published today in eLife, could be applied to the production of cultured meat grown entirely from cells, giving it a more realistic texture and flavour.
Cultivated meat has been making waves in the news lately, with reports from startup companies around the world developing cell-grown chicken, beef, pork and fish – mostly in early stages of development, not ready for large-scale production and with a couple of exceptions, not yet approved for commercial sale. Most of those products in development are in the form of an unstructured mixture of cells – like chicken nuggets rather than a slice of chicken breast. What is lacking is the texture of real meat, created by muscle fibres, connective tissue and fat – and it’s the fat that gives meat flavour.
In fact, consumer testing with natural beef of different fat content showed that the highest scores were registered for beef containing 36% fat.
However, producing cultured fat tissue in sufficient quantities has been a major challenge because, as the fat grows into a mass, the cells in the middle become starved of oxygen and nutrients. In nature, blood vessels and capillaries deliver oxygen and nutrients throughout the tissue. Researchers still have no way to replicate that vascular network at a large scale in lab grown tissue, so they can only grow muscle or fat to a few millimetres in size.
To get around this limitation, the researchers grew fat cells from mice and pigs first in a flat, two-dimensional layer, then harvested those cells and aggregated them into a three-dimensional mass with a binder such as alginate and mTG, which are both already used in some foods.
“Our goal was to develop a relatively simple method of producing bulk fat. Since fat tissue is predominantly cells with few other structural components, we thought that aggregating the cells after growth would be sufficient to reproduce the taste, nutrition and texture profile of natural animal fat,” says first author John Yuen Jr, a graduate student at the Tufts University Center for Cellular Architecture (TUCCA), Massachusetts, US. “This can work when creating the tissue solely for food, since there’s no requirement to keep the cells alive once we gather the fat in bulk.”
The aggregated fat cells immediately had the appearance of fat tissue, but to see if they truly reproduced the features of native fat from animals, the team carried out a series of further experiments.
First, they explored the texture, by compressing the fat tissue and seeing how much pressure it could withstand compared to natural animal fat. They found that cell-grown fat bound with sodium alginate was able to withstand a similar amount of pressure to fat from livestock and poultry, but the cell-grown fat that was bound with mTG behaved more like rendered fat – similar to lard or tallow. This suggests it could be possible to fine-tune the texture of cultured fat, so it best resembles the real-life texture of fat within meat, using different types and amounts of binders.
Cooking releases hundreds of compounds that add flavour to the meat, and most of those compounds originate from fat, including lipids and their component fatty acids. The team therefore examined the composition of molecules from the cell-grown fat and found that the mix of fatty acids from cultured mouse fat differed from native mouse fat. However, the cultured pig fat had a much closer fatty acid profile to the native tissue. The team’s preliminary research suggests it might be possible to supplement growing fat cells with the required lipids to ensure that they more closely match the composition of natural meat.
“This method of aggregating cultured fat cells with binding agents can be translated to large-scale production of cultured fat tissue in bioreactors – a key obstacle in the development of cultured meat,” says senior author David Kaplan, Stern Family professor of Biomedical Engineering at Tufts University and director of TUCCA. “We continue to look at every aspect of cultured meat production with an eye toward enabling mass production of meat that looks, tastes and feels like the real thing.”
Media contacts
Emily Packer
eLife
e.packer@elifesciences.org
+441223855373George Litchfield
eLife
g.litchfield@elifesciences.org
About
eLife transforms research communication to create a future where a diverse, global community of scientists and researchers produces open and trusted results for the benefit of all. Independent, not-for-profit and supported by funders, we improve the way science is practised and shared. In support of our goal, we’ve launched a new publishing model that ends the accept/reject decision after peer review. Instead, papers invited for review will be published as a Reviewed Preprint that contains public peer reviews and an eLife assessment. We also continue to publish research that was accepted after peer review as part of our traditional process. eLife receives financial support and strategic guidance from the Howard Hughes Medical Institute, Knut and Alice Wallenberg Foundation, the Max Planck Society and Wellcome. Learn more at https://elifesciences.org/about.
To read the latest Cell Biology research in eLife, visit https://elifesciences.org/subjects/cell-biology.
And for the latest in Stem Cells and Regenerative Medicine, see https://elifesciences.org/subjects/stem-cells-regenerative-medicine.